How to Build a Supply Chain Analytics Strategy
- Kwixand Team
- Apr 23, 2024
- 9 min read
Updated: Jul 8, 2024
Learn how to build a robust supply chain analytics strategy to optimize operations and drive efficiency. Explore essential components and actionable insights.
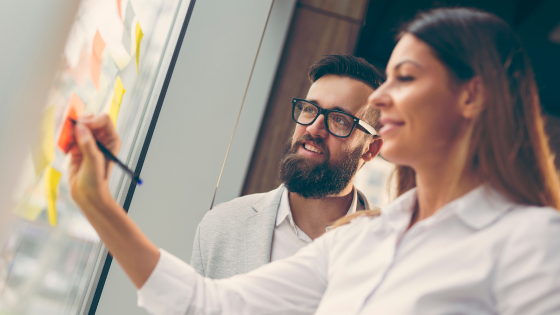
As a manufacturer, your ability to optimize operations, drive efficiency, and deliver value hinges upon your capacity to harness data-driven insights and embrace a culture of continuous improvement. In order to build a robust supply chain analytics strategy, there are several essential components that you should take into consideration. These actionable insights will help you understand your supply chain ecosystem and implement advanced analytical tools to empower your business to thrive in today's complex supply chain landscape.
Understanding Your Supply Chain
In the modern climate, supply chain disruptions have become increasingly prevalent, making it more important than ever for manufacturing companies to develop deep understandings of the intricate web of supply chains that crisscross the globe and many seemingly disparate industries. Each link in the chain, from raw material suppliers to end customers, plays a crucial role in shaping your operations and outcomes.
Here are 5 essential steps to help you gain a comprehensive understanding of your supply chain:
Map Out Your Supply Chain: Start by mapping out each step of your supply chain process. This includes identifying your suppliers, manufacturers, distributors, and end customers. Visual aids such as value stream maps or process flow diagrams can help you visualize the flow of materials and information throughout your supply chain.
Identify Key Stakeholders: Take stock of the key stakeholders involved in your supply chain, both internal and external. This includes suppliers, logistics partners, and even regulatory bodies. Understanding their roles and relationships within the supply chain ecosystem will help you anticipate potential bottlenecks or disruptions.
Assess Risks and Vulnerabilities: Evaluate the potential risks and vulnerabilities within your supply chain. This could range from geopolitical instability affecting raw material sourcing to disruptions in transportation due to natural disasters. By identifying these risks proactively, you can develop contingency plans to mitigate their impact on your operations.
Understand Customer Demands and Expectations: Gain insights into the demands and expectations of your end customers. This involves understanding their preferences, purchasing patterns, and evolving market trends. By aligning your supply chain strategy with customer needs, you can ensure timely delivery and enhance customer satisfaction.
Collaborate with Supply Chain Partners: Foster collaboration and transparency with your supply chain partners. Establishing open communication channels and sharing relevant data can help streamline operations and improve overall efficiency. Consider implementing technologies such as supplier portals or collaborative planning tools to facilitate communication and coordination.
By taking the time to understand the intricacies of your supply chain, you can identify opportunities for optimization and improvement. Whether it’s streamlining processes, reducing lead times, or enhancing resilience, a deep understanding of your supply chain will empower you to make informed decisions and drive success in your manufacturing operations.
Identifying Key Performance Indicators for Your Supply Chain Analytics Strategy
In your role as a manufacturer, tracking and measuring the performance of your supply chain is essential for driving efficiency and achieving your business objectives. Key Performance Indicators (KPIs) serve as crucial metrics to gauge the effectiveness of your operations and identify areas for improvement.
Here’s how to identify the right KPIs for your manufacturing supply chain:
Focus on Strategic Objectives: Begin by aligning your KPIs with your strategic objectives and business goals. Whether you aim to reduce costs, improve delivery times, or enhance product quality, your KPIs should directly reflect these overarching priorities.
Consider the Entire Supply Chain: Take a holistic approach to selecting KPIs by considering the entire supply chain ecosystem. This includes upstream processes such as procurement and production, as well as downstream activities such as distribution and customer service. By capturing the end-to-end performance of your supply chain, you can identify opportunities for optimization across multiple touchpoints.
Choose Quantifiable Metrics: Select KPIs that are quantifiable and measurable to track progress accurately. Examples of common KPIs for manufacturers include:
Inventory Turnover: Measures how efficiently you are managing your inventory by comparing the cost of goods sold to the average inventory value.
On-Time Delivery: Tracks the percentage of orders delivered to customers within the agreed-upon timeframe, reflecting your ability to meet customer expectations.
Production Efficiency: Assesses the productivity of your manufacturing operations by comparing actual output to planned output.
Quality Yield: Measures the percentage of defect-free products produced during the manufacturing process, indicating the effectiveness of your quality control measures.
Balance Leading and Lagging Indicators: Strike a balance between leading and lagging indicators to gain a comprehensive view of your supply chain performance. Lagging indicators, such as customer satisfaction ratings or order fulfillment rates, provide insights into past performance, while leading indicators, such as supplier performance metrics or production lead times, offer predictive insights into future outcomes.
Track Trends Over Time: Continuously monitor and analyze your KPIs to identify trends and patterns over time. Regularly reviewing KPI data allows you to spot potential issues early on and take corrective actions proactively.
By identifying and tracking the right KPIs for your manufacturing supply chain, you can gain valuable insights into your operations, drive performance improvements, and ultimately achieve your business goals.
Data Collection and Management
As a manufacturer, leveraging data to drive informed decision-making is key to optimizing your supply chain operations. Effective data collection and management processes are essential for accessing valuable insights and identifying opportunities for improvement.
Here are 6 essential steps to ensure robust data collection and management within your manufacturing environment:
Define Data Requirements: Start by identifying the types of data that are critical for monitoring and analyzing your supply chain performance. This may include production metrics, inventory levels, supplier performance data, and customer feedback. By defining your data requirements upfront, you can focus on collecting the most relevant information.
Utilize Automation Technologies: Embrace automation technologies to streamline the data collection process and minimize manual efforts. Implementing sensors, IoT devices, and RFID technology on the shop floor can automatically capture data on production volumes, equipment utilization, and inventory movements in real-time. This not only improves accuracy but also enables timely decision-making.
Integrate Systems and Platforms: Ensure seamless integration between your various systems and platforms to facilitate data sharing and interoperability. Connect your ERP (Enterprise Resource Planning), MES (Manufacturing Execution System), and SCM (Supply Chain Management) systems to create a unified data ecosystem. This integration enables data to flow seamlessly across different functional areas, providing a comprehensive view of your supply chain operations.
Implement Data Quality Controls: Establish robust data quality controls to maintain the integrity and reliability of your data. Regularly validate and cleanse your data to eliminate inaccuracies, inconsistencies, and duplications. Implement data governance policies and procedures to ensure data compliance and security standards are met.
Secure Data Storage and Accessibility: Invest in secure data storage solutions to safeguard sensitive information and prevent unauthorized access. Whether you opt for on-premises servers or cloud-based storage, prioritize data security and encryption protocols to protect your data from cyber threats and breaches. Additionally, ensure that authorized stakeholders have timely access to relevant data through user-friendly dashboards and reporting tools.
Monitor Performance Metrics: Continuously monitor key performance metrics related to data collection and management processes. Track metrics such as data completeness, timeliness, and accuracy to assess the effectiveness of your data management initiatives. Identify areas for improvement and implement corrective actions to enhance data quality and reliability over time.
By implementing robust data collection and management practices, you can harness the power of data to drive efficiency, optimize operations, and gain a competitive edge in today’s manufacturing landscape.
Analytical Tools and Technologies to Improve Your Supply Chain Analytics Strategy
Harnessing the power of advanced analytics is essential for manufacturers like you, looking to optimize your supply chain operations. Microsoft offers a suite of powerful analytical tools and technologies, including Microsoft 365 and Dynamics 365 programs, designed to empower you to gain valuable insights and make data-driven decisions.
Here’s how you can leverage these tools to unlock the full potential of your supply chain:
Microsoft Dynamics 365 Business Central: Business Central is a comprehensive solution designed to empower manufacturers like you to optimize your supply chain processes from end to end. With built-in AI and machine learning capabilities, Business Central enables you to forecast demand more accurately, optimize inventory levels, and automate procurement processes. Plus, its powerful tools for data manipulation, advanced reporting, and predictive analytics, enable you to analyze complex supply chain datasets and perform scenario analysis effectively. By combining Business Central with other Microsoft 365 applications such as Power BI and Power Automate, you can create seamless end-to-end workflows that drive productivity and efficiency across your manufacturing operations.
Microsoft Power BI: Power BI is a robust business intelligence platform that allows you to visualize and analyze your supply chain data in real-time. With Power BI, you can create interactive dashboards and reports that provide actionable insights into key performance metrics such as inventory levels, production efficiency, and supplier performance. Leverage Power BI’s intuitive interface and rich visualization capabilities to identify trends, spot anomalies, and drive informed decision-making across your organization.
Microsoft Power Automate: Microsoft Power Automate is a workflow automation platform that allows you to streamline repetitive tasks and processes across your supply chain. Automate data entry, document approval workflows, and notification alerts to improve operational efficiency and reduce manual errors. Integrate Power Automate with Microsoft 365 and Dynamics 365 applications to create seamless, end-to-end workflows that enhance productivity and collaboration.
Microsoft Dynamics 365 Supply Chain Management: Supply Chain Management is a comprehensive solution that enables manufacturers to optimize supply chain processes from end to end. With built-in AI and machine learning capabilities, Supply Chain Management empowers you to forecast demand more accurately, optimize inventory levels, and automate procurement processes. Leverage advanced analytics features such as predictive maintenance and intelligent resource scheduling to enhance operational efficiency and minimize downtime.
Microsoft Azure Machine Learning: Azure Machine Learning is a cloud-based platform that enables manufacturers to build, train, and deploy machine learning models at scale. With Azure Machine Learning, you can leverage predictive analytics to anticipate demand fluctuations, identify potential supply chain disruptions, and optimize production schedules. Integrate Azure Machine Learning with your existing Microsoft 365 and Dynamics 365 environment to unlock new insights and drive continuous improvement in your supply chain operations.
By leveraging Microsoft’s suite of analytical tools and technologies, you can transform your supply chain into a strategic asset that drives business growth and innovation. Embrace the power of data-driven decision-making to stay ahead of the competition and achieve operational excellence in today’s rapidly evolving manufacturing landscape.
Continuous Improvement and Optimization of Your Supply Chain Analytics Strategy
As a manufacturer, achieving operational excellence is an ongoing journey that requires a commitment to continuous improvement and optimization. By embracing a culture of continuous improvement, you can identify inefficiencies, streamline processes, and drive sustainable growth in your manufacturing operations.
Here are 6 ways you can foster continuous improvement and optimization within your organization:
Establish Performance Metrics: As detailed in the section above, developing KPIs and benchmarks to measure the effectiveness of your manufacturing processes is essential to your supply chain analytics strategy. Be sure to regularly review and analyze performance data to identify trends, patterns, and opportunities for optimization.
Encourage Employee Engagement: Foster a culture of employee engagement and empowerment by involving frontline workers in the continuous improvement process. Encourage employees to identify inefficiencies, propose solutions, and implement process improvements. Provide training and development opportunities to equip employees with the skills and knowledge needed to drive continuous improvement initiatives effectively.
Implement Lean Manufacturing Principles: Embrace lean manufacturing principles such as value stream mapping, Kaizen, and 5S to eliminate waste, improve productivity, and optimize resource utilization. Identify non-value-added activities and bottlenecks within your manufacturing processes and implement lean techniques to streamline workflows and improve efficiency. Continuously refine and iterate on your lean initiatives to drive incremental improvements over time.
Embrace Technology and Innovation: Leverage technology and innovation to drive continuous improvement in your manufacturing operations. Invest in advanced manufacturing technologies such as automation, robotics, and IoT sensors to enhance productivity, quality, and safety. Embrace digital transformation to digitize your manufacturing processes, enable real-time data analysis, and unlock new opportunities for optimization.
Implement Feedback Mechanisms: Establish feedback mechanisms to gather input from stakeholders and customers on your products and processes. Solicit feedback through surveys, focus groups, and customer satisfaction ratings to identify areas for improvement and prioritize initiatives accordingly. Actively seek input from suppliers, partners, and industry experts to leverage external perspectives and insights.
Iterative Improvement and Adaptation: Embrace an iterative approach to continuous improvement, where small incremental changes are implemented regularly to drive cumulative improvements over time. Monitor the impact of improvement initiatives closely and adjust strategies as needed based on performance feedback and changing market dynamics. Embrace a mindset of adaptability and resilience to navigate uncertainty and seize opportunities for optimization.
By prioritizing continuous improvement and optimization in your manufacturing operations, you can enhance efficiency, quality, and competitiveness while driving sustainable growth and innovation. Embrace the journey of continuous improvement as a strategic imperative for success in today’s dynamic manufacturing landscape.
Learn More About Supply Chain Analytics Strategies with Kwixand Resources
Looking for more ways to improve your manufacturing business? Explore Kwixand’s blog for additional expert insights and access past webinars in the Resource Library. Have specific questions on how your business can improve with digital transformation? Connect with a Kwixand expert today for personalized guidance on implementing supply chain analytics strategies and solutions tailored to your manufacturing needs.